 |

|

Takashi Ueda's Kinkarakami
Takashi
Ueda's quest to carry on the craft of gold-embossed wallpaper
Nobody knows exactly
when Spanish leather first arrived in Japan, but the oldest reference
to it is contained in a 1662 document called the Tokugawa Jikki.
The feudal lords and powerful landowners of Japan, who loved anything
novel, started to have their saddlery, scabbards and small cases
for personal items made from gold-embossed leather and it was not
long before the wealthy, fashion-loving townsfolk of the Edo Period
adopted the craft for such accessories as tobacco pouches. Many
examples of these can be found in museums and even antique shops
in Japan. The person who first tried to adapt the technique of calfskin
embossing to the manufacture of wallpapers using washi paper was
the talented mid-18th century entrepreneur Hiraga Gennai. Unfortunately
it appears that he eventually failed to improve the techniques to
the point that would allow for mass production. But in1877, at Japan's
first domestic Exposition, it is recorded that some nine manufacturers
were making gold-embossed leather- lookalike wallpapers using washi.
By this time Japanese artisans had refined the crafts of making
very fine strong paper, of carving and printing wood blocks (for
ukiyoe), of making very fine gold leaf and of urushi lacquering,
finally allowing the craft to become commercially viable.
|
 |

|
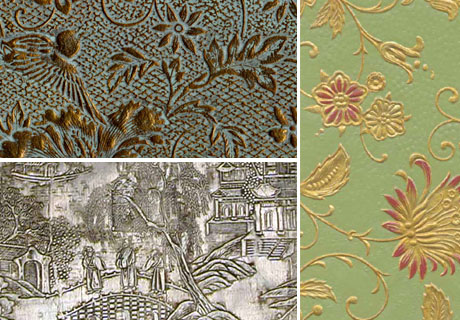 |

The 10 years from
1880 were the golden age of kinkarakawakami, as this craft of gold-embossed
wallpaper came to be known. At the time, Europe had a paper shortage
and British ambassador to Japan, Harry Parkes was assigned the task
of surveying paper manufacturing in Japan. Parkes's search resulted
in the dispatch of a massive batch of Japanese paper samples back
to England, among them kinkarakawakami. The product subsequently made
a huge hit in Europe. To keep up with demand the Finance Ministry's
printing bureau sponsored the craft, taking over all production. This
was the start of the craft's golden era. But it was a short-lived
one that lasted a mere 10 years, until about the time that the government
finally handed over production to the private sector. From this time
on -- at the end of the Meiji Era -- machine-made paper started to
be used in the craft, resulting in a drop in quality and a subsequent
lack of interest from Europe. Before long kinkarakawakami disappeared
from the market altogether. |
 |

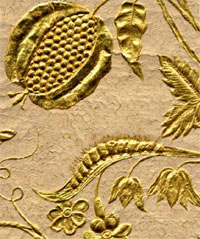 |
After the Second
World War kinkarakawakami made a brief reappearance, but this time
only as wallpaper for official and upper-class establishments in
Japan. It was used, for example, in the Diet building (Japan's parliament
house) and the VIP rooms of corporations related to the zaibatsu
industrial conglomerates as well as the homes of the very wealthy.
There was not enough demand to make an industry out of it and few
common people even knew it existed. Now, in modern times, Takashi
Ueda is the only person who has done anything to reproduce kinkarakawakami
or endeavor to preserve its techniques. To this end he continues
to devote all his energy.
|

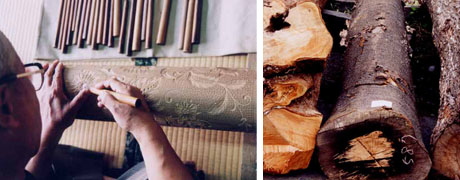
How
is it made?
The process is
first to adhere tin foil to washi paper and spray with water. The
paper is then wound onto a woodblock roller. One person stands at
either end of the roller and together they beat the paper with a
pig's hair brush for four to five hours until the design is firmly
and evenly applied -- a job of real dedication. All one can hear
from the workshop is the constant thwack, thwack, thwack of this
work going on. The paper is then dried in the shade. Two layers
of backing paper are applied and the surface design is tinted with
colored urushi lacquer. A final coating of clear varnish makes the
tin foil shine just like gold leaf. In some cases, real gold and
silver leaf are actually applied. In such cases the gold leaf is
not gaudy, but quiet and elegant, while the silver leaf can be treated
to acquire a stylish tarnished look. It takes two weeks to complete
a piece of wallpaper of 60 sq cm. At Present Mr Ueda is doing this
work with the help of three graduates from the Tokyo University
of Arts, Kazuhiro Ikeda, Hiroshi Goto, and Yuhei Nagira, who were
each drawn by Mr Ueda's enthusiasm for this craft. Returning briefly
to the subject of the cherry wood rollers (diameter about 20cm,
length 120cm) that first piqued Mr Ueda's interest, Mr Ueda has
since attempted the creation of new designs of his own. This required
him first to visit timber yards to search for just the right type
of cherry wood for the woodblock rollers and then to commission
a shrine carpenter-trained transom carver to carve them. The cost
of one roller is no less than 5 million yen. In most cases, however,
he borrows the old rollers - of which there are 117 - from the paper
museum.
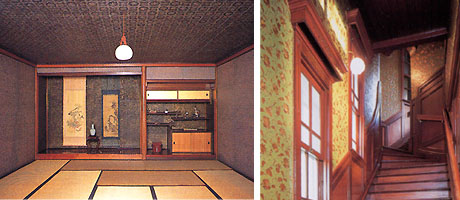
|

Restorations around
Japan
Mr Ueda has been
involved in several wallpaper restoration projects until now, including
the reception room of the NYK Line Co, Ltd.'s Otaru branch office
in Hokkaido (1985), the former Hayashi Home in Okaya City, Nagano
Pref. (1991), the Kure Irifuneyama Memorial Pavillion in Kure City,
Hiroshima Pref.(1995), Ijohkaku Pavillion in Kobe City, Hyogo Pref.
(1999), and the former Iwasaki Home (2002).
Of all of these restorations the most interesting is perhaps the pure
Japanese hanare (detached room) of the former Hayashi Home in Okaya,
itself a precious legacy of the glory years of the early Japanese
silk spinning and weaving industry. The gold-embossed wallpaper is
applied to a feature wall and the ceiling of the second floor of this
structure. It is open to the public and anyone wishing to visit should
call the Education Committee of Okaya City at 81- 266-23-4811.
|
 |
 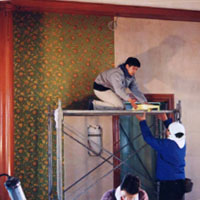 |
For Mr Ueda's three apprentices such restoration projects have not
been just a matter of acquiring techniques, but a precious opportunity
to examine old examples of karakami and try to reproduce them. However
there have been very few people interested in having kinkarakawakami
made for newly built structures. Two of Mr Ueda's commissions for
modern structures have been the VIP room of an arts complex, the
Tokyo Geijutsu Gekijo, in West Ikebukuro, and the director's office
of the Children's Education Center, but neither place can be viewed
by the general public. There is something very special about the
beauty of white plaster or cracked earthen walls, and being in a
room surrounded by the elegant perfection of Kyoto-style woodblock-printed
wallpaper is also a very special feeling, but I wonder if there
are no architects interested in applying Mr Ueda's kinkarakawakami
to the interior of modern structures. They may find the contrast
extremely effective.
The future
Mr Ueda calls
the wallpaper he makes using techniques gleaned from the sparse
sources available and from his own research and trial and error,
kinkarakami, shortening it from the original kinkarakawakami. But
if there is no one who wants to use it there is no way to continue
making it. It is thought that all the renovations using kinkarakawakami
in Japan have now been completed so Mr Ueda's big question is how
he can carry these rare techniques on for posterity. He sells small
boxes and scrolls and framed examples of kinkarakami at such outlets
as the Edo Tokyo Museum shop, but this provides far from enough
work for the young apprentices who wish to carry on the trade. All
Mr Ueda can do is wait and hope that a chance will come for renovation
work overseas or to put the techniques to use in new buildings.
Mr Ueda would like to talk to anyone who is serious about acting
as an agent for kinkarakami overseas.
(March
2003, Yuko Yokoyama)
|
|
to
the shopping page
|
|
|
 |
 |