 |
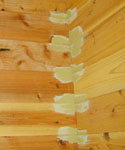
Holes and irregularities on the wall and especially around the door and windows are puttied for a smooth finish. |
 |
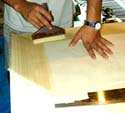
Washi is stacked on top of each other, sliding 3mm apart from one corner. Starch glue is applied with a brush from the back. |
 |
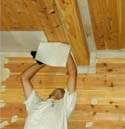
After the "mawari-beta" process, the first layer is papered. The young master paperhanger bends his back like an acrobat to paper the ceiling, but confesses, his back aches after the end of the day.
|
|
|
The workmen arrive early in the morning. They left at 4:30 a.m. from Tokyo, to avoid the traffic jam with everyone leaving for summer vacation. They reached Uminokuchi, Nagano prefecture by 7:30 a.m. I welcome them with tea, they took a short break to stretch their legs. The experts wasted no time and eagerly jumped to work.
First, the preliminary arrangements. All wall sockets, lighting fixtures are removed. Before proceeding with the papering, the warped horizontal wooden boards are planed. Putty is applied to all defects and irregularities, and around closet and window frames for a smooth finish.
Once that is done, the next process called "mawari-beta" begins. Starch glue is applied onto a narrow washi strip of approximately 8 cm width, and pasted around the closet opening and window frame. The glue is made from tapioca starch mixed with adhesive bond. The washi strips are secured by smoothing the surface with a firm brush made from hemp palm, in rhythmical strokes and tapping.
For "fukuro-bari" or the intriguing hollow papering method, the base mounting must be prepared. The paper is cut out into 2 x 3 "han" (606 cm x 909cm) rectangular sized sheets with a sharp cutting tool. Two of the edges will have a straight edge. The remaining two edges are torn by applying moisture to the paper. By dampening the edges with water, the cut edges will have a fuzzy finish caused by the raised fibers of the washi. Next the washi are stacked into a pile of about 20 sheets. Every other sheet is dampened by brushing water on the surface, and laid on top of each other. The two edges of each sheet are visible, as they are stacked sliding them approximately 3mm apart from one corner. The reason why washi is dampened is so that the washi will be very tightly hanged as contraction occurs as it dries on the wall. Next glues with different consistency are prepared. On the straight edges, a thick coating of glue and on the torn fibrous edges a lighter coating of glue is required. Each sheet is tautly pasted in place aligned in a straight row. Washi is positioned to overlap the adjacent paper by one "sun" (Japanese inch). Careful calculation is made so that the overlap of the fibrous edge over the adjacent sheets straight edges does not create a ridge. These skills come from absolutely knowing the capabilities of washi and fully utilizing the characteristics of the fine fibrous texture.
The thick glue is applied over the overlapping area on the narrow strip surrounding the door and window frame.Å@The washi sheets are smoothed starting from the torn fibrous edges with overlapping seams. The fukuro-bari sheets are actually like envelopes, with the middle of each sheet floating with only its edges attached to the wall. The word "fukuro bari" (or "pouch pasting") derives from this unique pasting method. The pasted overlapping seams of each sheet as well as over the narrow strips are called "koge-tsuki". The floating sheets are secured to the walls by each "koge-tsuki". The hollow pocket created between the wall (ceiling) and washi is the secret behind how a consistent temperature and humidity within the room is maintained. Washi has amazing quality to insulate as well as breathe. For this reason, the air in rooms utilizing washi for fusuma (sliding doors) and shoji screens is often said to have an indescribable warmth and serenity.
After the ceiling is finished, next comes the "fukuro-bari" papering on the walls. The young master paperhanger asks me to decide whether to hang the sheets horizontally or vertically. I shyly suggest "can we try a horizontal brick pattern?" "Each sheet must be positioned halfway between the sheets above and below. By starting from one side of the wall, and working the way across to the other end of the wall, the leftover sheet will require trimming after fitting at the corner. The remaining sheet is cut and placed onto the next row. In this way, the overlapping seams do not align perfectly in the middle of the row above, but create a pattern something similar to a brick wall." Unsure what the master's reaction would be, I add "and in this manner, handmade paper do not go to waste." The master was quite enthusiastic with this idea, and I, just ecstatic and relieved. On a side note, the Chinese character " hari, bari " used in "fukuro-bari" does not use the word "hari" which means "to paste" but uses the Chinese character "haru" which signifies to tauten or tighten". "Fukuro-bari" is in fact a "pun on words" playing with words accentuate the fact that the sheets must be positioned tautly. Paperhanging skills seems to have something in common with the Japanese traditional crafts work and hand works as there seems to be a meaning behind every simple act and are impenetrable.
The first day finished here as scheduled. The room is ready to be lined with the top layer tomorrow.
*The Bon Festival traditionally took place for several days around July 15 on the lunar calendar, when the souls of the dead are believed to return to their earthly homes. These days it is usually held around August 15. Many people make trips back to their hometowns at this time of the year to visit the graves of relatives. During this festival people set up lanterns to guide the souls of the dead to and from their homes, and prepare a special feast of vegetables for the returning souls. Bon odori, or hypnotic outdoor dancing is held everywhere. In many villages, on the last night, lanterns are set adrift on rivers (sea) to guide the spirits back across the seas.
*tatami = tatami mats are six by three feet straw mats
|
 |